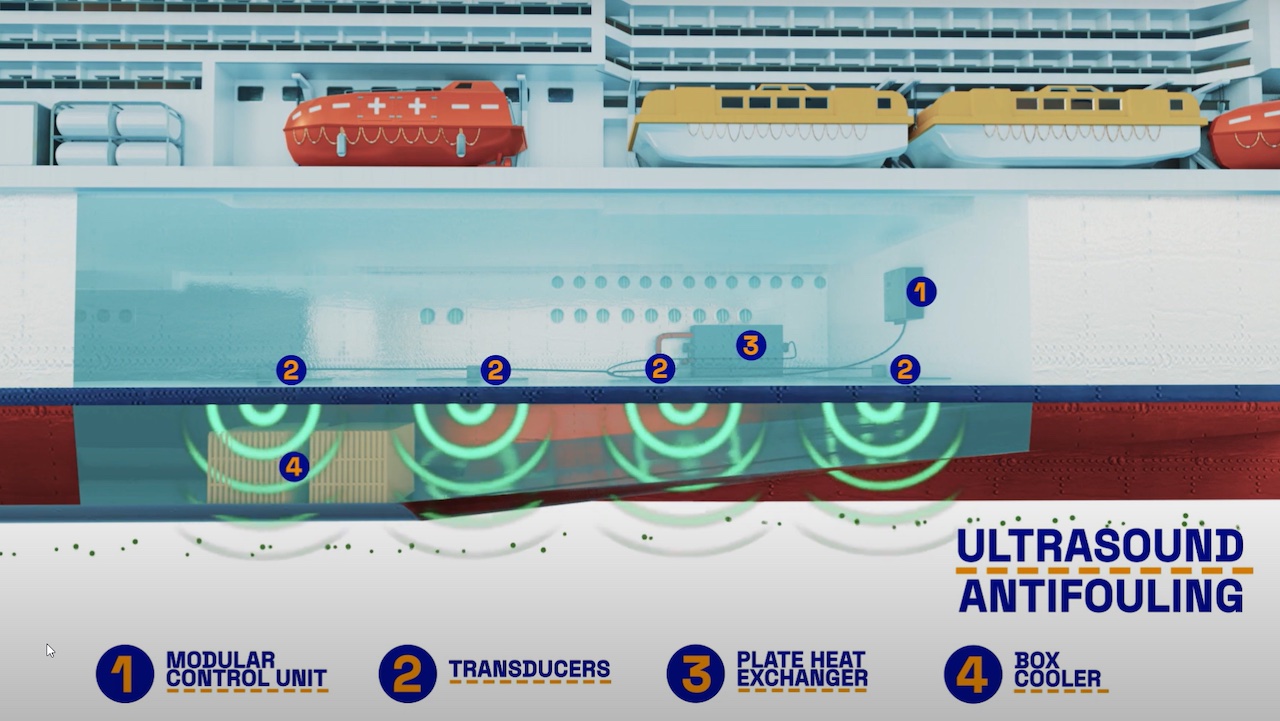
The use of acoustic waves in the ultrasound range (frequencies higher than 20 kHz) is a non-toxic and environmentally friendly solution for preventing biofouling on vessels’ hulls and niche areas. This revolutionary idea, conceived in the 1960s, is now taken forward with HASYTEC's groundbreaking advancements in the maritime sector. Within the CHEK project, we are transforming our Dynamic Biofilm Deposition intelligent (DBPi) system, originally designed to protect ship niche areas, like propellers and sea chests, to provide comprehensive hull protection.
The HASYTEC system automatically detects and sets the optimal frequencies for each ultrasound transducer, thanks to its intelligent sensors for temperature, current, and voltage. Once the resonant frequency is identified, a pulsed ultrasound signal is emitted, causing vibrations along the hull. The intensity of these vibrations depends on factors such as material type, thickness, and the input power used. After the initial excitation, compressional and shear waves in the solid are typically observed. The oscillators of a compressional wave vibrate in the direction of propagation whereas those of shear waves vibrate perpendicularly to it. As the vibrations generate compressional and shear waves, a series of mechanisms work together to prevent biofouling. Disruptions at the solid structure-water interface impede the initial cell adhesion process, while the pressure oscillations created by the ultrasound, known as acoustic streaming, further disturb the fouling process.
With the implementation of the HASYTEC ultrasound antifouling technology in the global fleet, there will no longer be a need for antifouling paints, typically containing heavy metals. By eliminating the toxic streams, our system promotes environmental sustainability and also reduces operational expenses and maintenance on board.
For more information about ultrasound antifouling technology, please see this video.
D6.5 Ultrasound antifouling concept and installation design
The objective of this deliverable D6.5 was the creation of a conception and manual for the installation of an ultrasound antifouling system for hull surfaces and niche areas based on the construction plans of the two selected demonstration vessels. For this purpose, these installation concepts for the application of an ultrasound antifouling system were designed and subsequently the installation plans were created and provided to the involved consortium partners. The deliverable provided an introduction to biofouling, how environmental conditions affect the rate and the overall impact it has on ships operational efficiency. It includes a brief literature review, followed by a description of a simulation run that describes the wave propagation in structural steel. Here, the Finite Element Analysis (FEA) modelling approach was used and simulations were run using ANSYS Mechanical 2022 R1 in a Coupled Field Harmonic analysis. The modelling results provided information on the minimum power required to keep the sonicated area free of biofilm and allowed for further optimisation of positioning and required numbers of ultrasound transducers for the hull application. In addition to the technical drafts for an ultrasound antifouling system, suitable coating types for non-biocide antifouling paints were also investigated to determine the best possible fit with the ultrasonic antifouling.
The deliverable then illustrated a conceptional antifouling method using ultrasound. Detailed technical specifications of the HASYTEC ultrasound antifouling system were given and the installation concepts for the niche areas and the hull application were provided, as well as technical drawings, adapted to the two case vessels chosen for the Bulker case vessel and the Cruise Ship case vessel. Main task within the work package WP6 and the deliverable work scope was to determine the optimal and best possible transducer placement and ultrasound transmission to be able to achieve the most effective results. Under this aspect, specifications on transducer placement and installation were outlined, which will have to be proved during the trial voyages conducted in WP7. Established results will enable HASYTEC to generate a matrix that can be provided for third party (e.g. naval architect or shipyard) calculation and commissioning process. Trial voyage results, adjustments and improvements of the prototypes and generated matrix will later feed into the Digital Twin step in simulation model generation and finally into the Future-Proof Vessel Design platform, enabling a general and overarching review of the effects achieved with HASYTEC ultrasound antifouling systems as an environmentally friendly and advanced technology. With this deliverable HASYTEC provided guidance on how the ultrasound system can improve the hydrodynamic performance of vessels. Biofouling increases in particular the hull roughness of the vessel and thus also the fuel consumption. The aim of the CHEK project is to decarbonise long-distance shipping using technologies from the consortium. The prevention of biofilm and deposits with ultrasound contributes to this goal. Schematic and technical drawings were provided for the two case vessels. They include details on the HASYTEC antifouling system installation so that optimal sound transmission could be achieved and biofouling prevented. Good and bad practices as well as a full description of the hardware and software specification were described. The installation concept will be used as a framework for future installations. The preparation of this document was done in conjunction of D6.7 for the prototype construction. Results will be examined in real life test in WP7 during a 7-month demo voyage period and final outcome will contribute to the evaluation of the whole project.
D6.7 Ultrasound antifouling prototype
The objective of the deliverable D6.7 was the development and production of ultrasound prototypes for the hull and niche areas, which will be tested in real life on the demonstration case vessels in WP7. The report provided an overview of the development of the hardware and software for the prototype systems. The simulations and laboratory tests have shown that a higher ultrasonic power is required for good area coverage and ultrasound output power. To achieve this performance requirement, both the hardware and the software were adapted. For the hardware, this was achieved by adjusting the supply power as well as by newly developed ultrasonic transducers. Work on the technical configuration involved the adaptation of the systems to changing environmental conditions present in vessels, upgraded internal and external system communication and software updates. All methods required several design and prototyping iteration loops to achieve the desired results.
Following the development process, the prototypes for transducers and control units were manufactured at HASYTEC´s own facilities. Quality of the production was tested and proven with Factory Acceptance Tests (FAT) for hardware and software , which evaluated the equipment during and after the assembling of the prototypes. The FAT verified that the prototypes were built and will operate in accordance with the design specifications.
The main task of D6.7 was the actual prototype development, manufacturing and testing. The prototypes proved to be working following all required measures based on the factory acceptance tests, and were ready to be installed on the two selected demonstration vessels. Prototypes for the WP7 installation were developed and produced for niche areas and hull test patches. For the niche areas, in particular the software was adapted to generate the best possible ultrasound power and to keep them free of biofilm and other deposits. In addition to the software, hardware adaptations were also made for the Intelligent Hull Protection prototype (IHP). New functions for communication with the ultrasonic transducers were enabled so that important factors such as temperature and position can be monitored. Newly developed ultrasonic sensors have improved ultrasonic performance and are expected to keep a potential test area of ~40m² free of biofilm as shown in D6.5 Ultrasound antifouling concept and installation design. Following the development, FATs were performed on the hardware and software. These hardware tests ensured that a continuous power supply is available for the application to be tested. The future operational data are recorded by data loggers for later evaluation, and unexpected errors can be detected or the data for WP2 can be included in the creation of a digital twin.
D6.9 Manual on installation of ultrasound antifouling on real vessel
The report extensively discusses the implementation, installation, and commissioning of ultrasonic antifouling systems on ships, focusing particularly on hull protection. Through the trial voyages on two case vessels as part of work package 7 (WP7), the HASYTEC ultrasonic antifouling prototypes were evaluated, highlighting the challenges of this labor-intensive and cost-critical application. The findings from these evaluations are intended to serve as the initial basis for a matrix designed for third-party use, such as naval architects and shipyards, to facilitate calculation and commissioning processes.
Key aspects covered include the detailed process of conceptualizing, designing, and deploying ultrasonic-based antifouling systems. The importance of correct installation is stressed, with specific attention to work planning, preparation, and integration with existing hull structures. The report incorporates constructional drawings and organizational tools like the Work Breakdown Structure (WBS) and the Critical Path Method (CPM) to ensure efficient resource allocation and optimal scheduling for ultrasound integration.
Moreover, the report elaborates on creating a comprehensive matrix or manual that could aid shipowners and operators in assessing the cost-effectiveness and performance benefits of these systems, considering factors like vessel size and other constructional parameters. The deliverable D6.9 outlines the procedure for manual installation of ultrasound antifouling systems, focusing on the optimal placement of transducers to maximize effectiveness.
In conclusion, the implementation of ultrasound antifouling systems represents a significant enhancement in ship maintenance practices, providing a sustainable and environmentally friendly alternative to traditional methods. The report underscores the potential of these systems to improve ship efficiency and reduce operating costs while minimizing environmental impacts.